What is Casing Drilling (Casing while drilling, CwD)?
The concept of drilling and casing the hole in the same time is, of course, valuable by combining two time consuming processes. So how is it possible? What are the limitations? What are the challenges? And what are the benefits?
In a nutshell
The main purpose of Casing Drilling, or Casing while Drilling (CwD), is to eliminate classic casing runs and isolate formations while drilling. By using Standard casing string instead of conventional drill string, the drilling and casing are executed simultaneously, section by section. Casing while Drilling is also a hazard mitigation solution, having applicability in drilling soft shallow sections with high borehole instability and known losses.
How is it performed?
The introduction of the casing running tool (CRTi) has made way for Casing Drilling. When the casing is run with top drive and CRTi, you are able to operate the casing string much in the same manner as a drill string. The top drive casing running tool (TDCRTi) lets you push, pull, rotate and reciprocate, thus giving you extended control over the string.
Read also: Top Drive Casing Running – why would you look for anything else?
On level two, CwD is used drilling vertical wells with non-retrievable bits, mostly for surface and soft sections. On level three, CwD is used drilling directional with casing, with retrievable BHA’s, mostly for deeper and challenging sections.
What are the benefits?
- Maximizing efficiency
- Two operations in one, each meter drilled will be cased.
- Reduces time for tripping in and out, and the risk involved with it.
- Improves drilling efficiency by reducing of the non-productive time.
- Drilling time and cementing saving.
- The smearing effect: Prevent and cure (or minimize) losses while drilling, i.e. good control of the annular pressure losses.
- Applicability in depleted zones or underbalanced drilling applications.
- High applicability in drilling soft shallow sections (high borehole instability with known losses).
Is it for me?
What will decide if CwD is suitable for a specific project?
- Geology.
With level 2 CwD (using drillable bits) most surface sections are suitable for casing drilling. These sections are characterized by various layers of clay (or marl), sand, conglomerates, gravels, sandstones, coals. However a detailed analyse is required in order to select the most suitable casing drilling bit (PDC type) for your section. - Rig type
- The rig has to be equipped with a top drive
- Efficient pump system and mud system is required
My experience from more than 60 projects shows that Casing while Drilling is an effective method in minimizing drilling time and costs, and makes this technology profitable both time- and cost wise. The benefits of combining two operations in one are obvious, but I would also like to emphasis the reduced cementing costs. The smaller annulus requires less cement and has less cement excess compared to conventional drilling. CwD also improves the QHSE performances and can be executed with fewer POB.
Simply put, CwD is highly profitable for the modern drilling industry, even in a softer price environment, by maximizing the efficiency in delivering a quality well.
Topics: Casing drilling
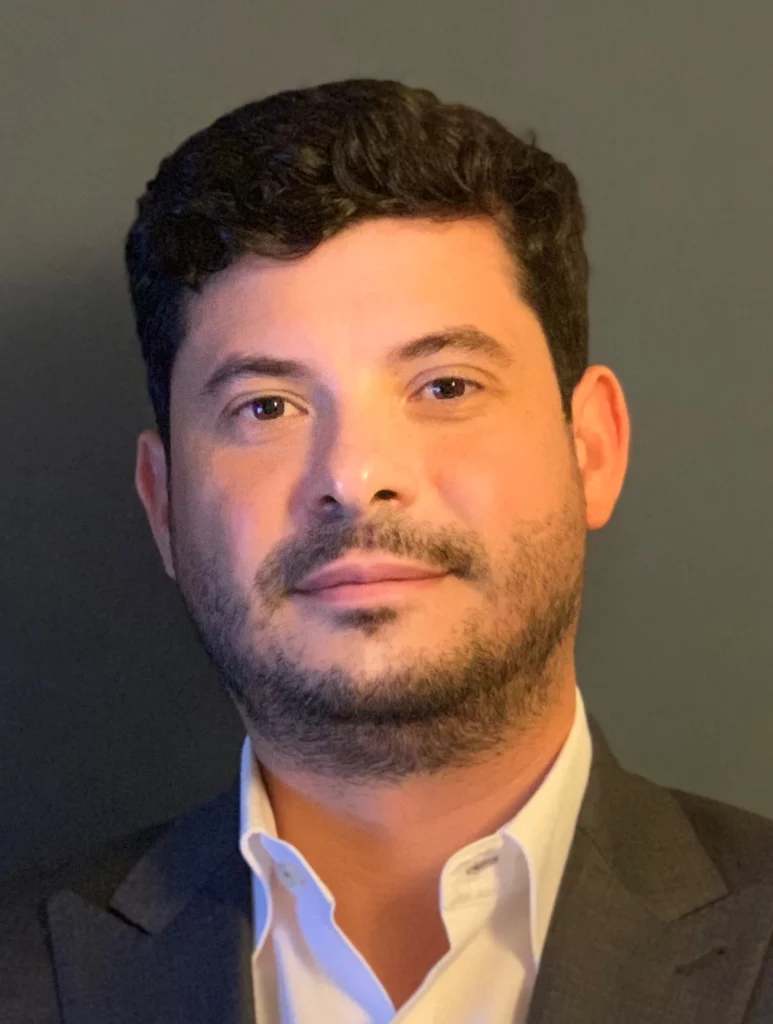
By: Alexandru Gomoescu
Alexandru has been in the oil and gas industry for ten years providing drilling related services such as casing drilling, tubular running and drilling equipment rental. He is now Regional Manager (CESEE) at Odfjell Well Services.