Tubular handling with care: Running any production riser with standard equipment
The days of specially designed equipment to take care of demanding tubular handling, like prod risers, are over. Clients now get the benefit of using standard equipment to handle even the most oddly dimensioned and fragile tubular safely.
At OWS, we have recently been involved in two projects where demanding prod risers have put extra challenges on the handling. Both on Snorre A and Heidrun we have run prod risers that in past times would call for equipment specially made for just that riser. Needless to mention what that would mean regarding flexibility, planning, and costs for the client.
Soft, flexible steel
Both on Heidrun and Snorre A we faced Tension Leg Platforms with the deepest wellhead on 350 meters. The prod risers in these rugged areas of the North Sea needs to be flexible to cope with excessive deviation up to 50 meters.
Softer steel is more flexible but also more susceptible to scratches and outer damage. A rift in the tube would most certainly lead to corrosion, so the handling when mounting and screwing the tubing was decisive. Considering a lifespan of 15 to 20 years, you can imagine how a scratch would expose the steel to potentially vicious corrosion.
A tube like that is heavier than other tubings. The joints are also longer. Particular care must be taken during transportation and mounting to avoid any damage whatsoever.
The TRS crew need to be trained for these kinds of installations, and you would look for a mindset of extra care and thoroughness. And you need to keep the sink spray available for all parts of the process.
Imroved casing running starts with proper training of the casing crew
New challenges
Installing and making up such a tube is challenging in many ways:
- The soft steel is less resistant to outside damages like
- scratches from contact with other materials
- crushes from the dies gripping the steel
- The OD may differ as much as 1/4 – 1/2″
- The make up torque is different, demanding optimization of the torque turn software.
- The threads need to be absolutely free of polluting elements
Solid but gentle
How to get a solid grip on the OD without harming the soft and flexible steel? One of the advantages of having our own equipment is that we can modify it to fit a variety of purposes.
To keep below the crushing factor, we fit the Flush Mounted Spider (FMS) with dies specially designed for that purpose. These are lo marking dies that distribute the force evenly and on a larger area than normal dies.
Being able to cope with the different ODs, we would set up a variety of sizes to quickly fit the OD at hand.
Read more: The use and misconceptions of slips in casing operations
Modifying the torque turn software
Programming the Torque Turn Software is a part of every TRS job. The computer-controlled torque turn software is in that way very flexible and can adapt to different casings by just entering the relevant specs for the casing to be run.
On Snorre A, however, we ran into a slightly more complicated task. The makeup should not be optimum torque, but delta turn. The remote operated MU-tong would not stop at a defined torque, but rather after a 40-degree turn. Again, the flexibility of the tools came to our rescue as our engineers rewrote the software code to fit the task at hand.
Flexibility
The tubular handling on these two projects illustrates how clients now can expect their TRS company to deliver flexible and cost effective solutions no matter what kind of tubing they face. Well engineers should be confident that they can design the well the way the circumstances predict without the TRS company having to build new equipment, jeopardizing schedule and budgets.
Topics: Tubular handling
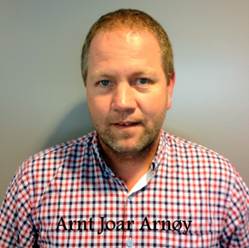
By: Arnt Joar Arnøy
Arnt Joar Arnoy has more than 25 years’ experience from the oil and gas industry. Holding positions as Workshop Mechanic, Service Technician offshore, Operation Engineer onshore. He is currently Operation Manager for OWS in Norway.