The importance of Magnets in a Wellbore Cleanup String
The use of magnets has proven to be a simple, cheap and effective way of removing metal debris from a well. Every WBCU operation should include magnets.
Why magnets are indispensable
During the completion installation, metal debris can cause a lot of trouble, especially if it gets jammed in downhole valves and causes cuts and tears on rubber seals. Some logging tools have powerful magnets, and if there is metal debris in the well, it can stick to the tool and interfere with the readings.
Needless to say, these are unwanted situations that need to be avoided. Since steel is a high-density material, it can be difficult to circulate it out of the well. This is why magnets are so great. They work on the law of attraction, attaching swarf and metal shavings to themselves for safe removal on the surface.
The use of magnets over the years
There’s been a trend over the years to run more and more magnets in the wellbore clean-up string. Whereas one magnet per casing size was common, it is common now to run three magnets in the string to improve cleaning.
We have also seen a trend to move away from using filter tools as the primary means of cleaning the well. 10 years ago they were very popular and would always be full of all kinds of debris from gunk and small, fine sands to tong dies or worse. Now they seem to catch less and less debris. Why?
The main reason is that methodology and technology has improved in chemical and hydraulic displacements which means the gunk and sands are being carried out by the clean-up fluids. But what is left behind? It is nuts, bolts, perforation burrs, filings from the casing and the like. Basically metal!
That does not mean that filters do not have their place. They do and that’s a topic for another day, but the trend is a greater focus on high strength and high capacity magnets, combined with an effective chemical and hydraulic clean-up.
The evolution of the magnet as a wellbore cleaning tool
Downhole magnets have evolved so much over the years. If you don’t believe me just do a Google Patents search of the term “downhole magnet”. In the last five years they are becoming longer with higher capacity and are including more exotic materials rare earth elements to increase strength and temperature range.
Even the shape of the magnets are evolving from cylindrical shaped tools to the far more efficient star shaped design. At Odfjell Well Services, we prefer the star shaped tool bodies where the magnets are arranged in ribs (like the MAGStar4™ HD Casing Magnet). Star shaped magnets are more efficient, because the well fluid has to pass between rows of magnets, rather than passing a sleeve, which provides better attraction. Furthermore when being pulled to surface the ribs protect the debris and prevent it from falling off. We believe star type magnets are the best and continue to invest heavily in them.
> Read also: How to do BOP and marine riser clean up in fewest possible runs
Current trends in P&A in the North Sea
The traditional wellbore clean-up market has been pre-completion clean-up operations (the front end of the lifecycle of the well), however as North Sea assets move to the end of their life cycle, we see an increase in use in magnets for recovering casing and heavy milling for P&A operations.
According to The Engineer, almost a thousand North Sea oil wells will be decommissioned over the next decade.* That means thousands of plugging and abandonment operations and a huge increase in metal debris recovery from wellbores.
P&A is still in its infancy, and a big industry is sprouting up around how to reduce the costs connected to it. Magnets will undoubtedly, pun intended, stick around for the long run as an important tool in wellbore cleanup operations.
The good thing about magnets is that you could never accuse them of not doing their job, cause they always come back with something on them. And sometimes it could be surprise.
Topics: Wellbore CleanUp
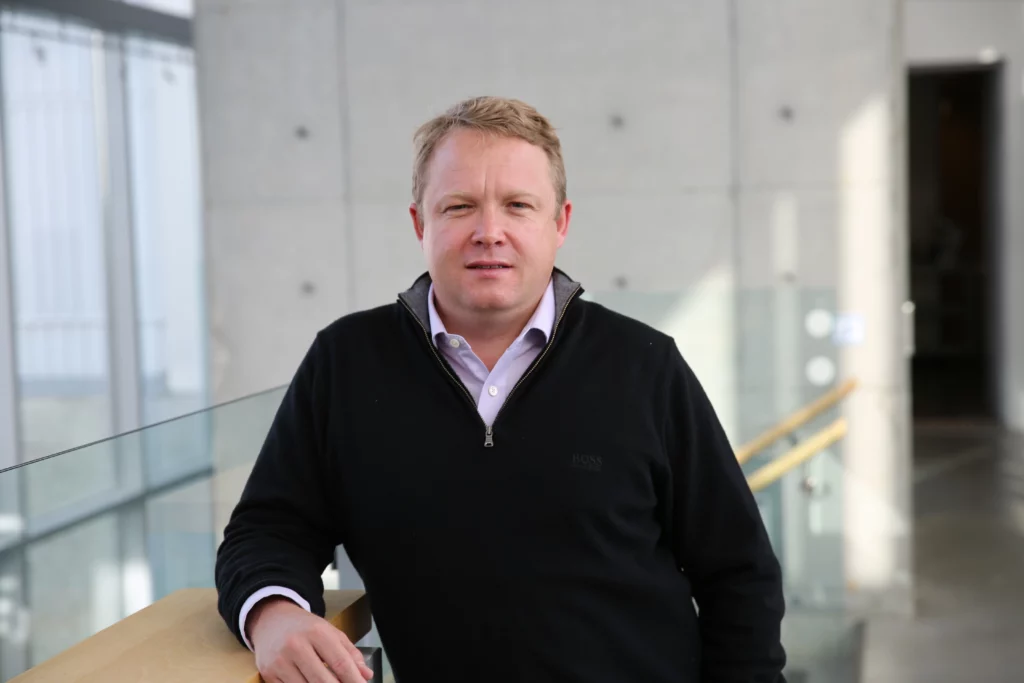
By: Simon Leiper
Simon Leiper has worked in the wellbore clean-up industry for 15 years. He leads the wellbore cleaning product line with Odfjell Well Services and is the inventor of multiple Odfjell patent applications. He has an HND in Mechanical Engineering and has worked and lived in international locations.