TFA challenges in top hole drilling
There is always a discussion about where to put the most flow, through the bit or through the hole opener. There are as many points of views on this topic as there are specialist working with top hole drilling.
The question is – when 20% of the opening effect comes from the bit and 80% comes from the hole opener, shouldn’t that be reflected in the flow distribution?
TFA issues in top hole drilling
Total Flow Area, or TFA, is the description of the liquid flow going through the string and coming out through the nozzles in the bit and the hole opener. In top hole drilling we use seawater. The seawater keeps the equipment clean and transports the cuttings out of the hole, thus preventing balling. In order to keep both bit and hole opener at optimum functionality, the distributed flow must split between the two. The ultimate question being how much flow on the bit, and how much on the hole opener.
How to deal with boulders while drilling?
Before the Boulder Buster family was launched, we all used conventional style hole openers. They handled the job with great success for 20 or 30 years, and they still do. A typical distribution of TFA used up to five-six years ago was 70% on bit and 30% on hole opener.
However, more demanding drilling operations, in areas such as the Norwegian Sea and the Barents Sea, meant that we had to think differently regarding top hole drilling. These new areas needed a hole opener with more weight to improve vertical top hole drilling, and a cutter design to withstand heavy boulders and rough formations.
A new hole opener, with a unique cutter, designed for more efficient drilling busted its way into the market in 2010. The Boulder Buster demanded more flow for optimal operation.
>Se also: Hole openers: When your black gold is between a rock and a hard place
Drill faster, get more cuttings!
What happens when you get a tool that can manage higher RPM and more weight? Yes, you drill faster, but you remove more mass and get more cuttings that you need to bring out of the hole. The hole opener removes 82% more mass than the bit, and it is supported from the flow coming out of the bit. But is it enough? The manufacturer/designer of the Boulder Buster recommends 70% of the flow to be put on the hole opener and leave the remaining 30% for the bit. Reality is that this specification collides with client’s opinion. They are concerned about the bit being balled and are unwilling to split more than 50/50.
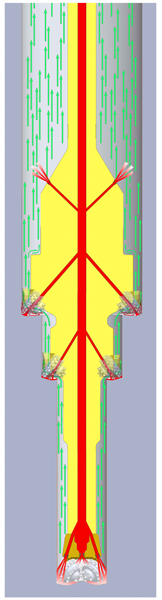
Showing areas cut by a hole opener with stages of 17,5″, 28″ and 42″. The high pressure fluid (red) scours the rock face ahead of the cutters and should be distributed according to the area being cut in order keep the ROP up. Favoring the bit with a higher volume of fluid reduces fluid to the other cutters and can decrease ROP and adversely affect the life of those other cutters.
Soft or hard?
Unfortunately, we cannot expect the formation to be just pebbles and gravel. When you drill in soft formations with clay, for instance, you need to adjust the nozzle size to ensure the flow doesn’t wash out the formation. A small nozzle produces higher pressure, while a big one covers larger areas with lower pressure.
Time on our side
The experience from decades of conventional hole openers is hard to overlook. But the Boulder Buster sets new standards, and the process needs to be adapted to the new tool. To give it optimal working conditions, more flow must be distributed to the hole opener. I believe it’s just a matter of time before we see the magic 50/50 limit being crossed.
Topics: Drilling Equipment, Drilling, Down Hole
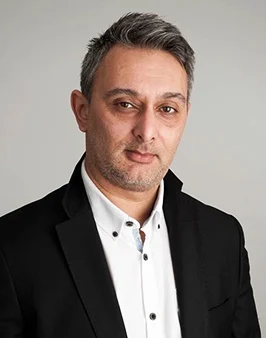
By: Trond Inge Mitchell
Seven years as NDT inspector for bottom hole equipment, tubular, casing, og and handling equipment. Seven years as in-house tool coordinator for OWS, logistics, equipment and customer contact/supervision. Two years as sales representative for OWS equipment. Customer contact, supervision, follow-up, etc.