Next-generation downhole tools will revolutionise the North Sea market
Innovative combination of design and performance will facilitate highest ambitions across legacy assets, writes Ian Low, Product Line Manager – Well Intervention with energy services company Odfjell Technology
The North Sea offshore oil and gas market includes a large number of legacy assets for which operators and service companies require proven solutions to carry out a range of downhole operations.
From plug and abandonment (P&A) to remedial and recovery services, the future of this existing infrastructure is challenging the industry to adopt more cost-effective processes based on better practices and improved tools.
Efficient, effective and safe casing magnet operations are an integral part of this formula – removing ferrous debris during workovers and in advance of the damage it might cause to completions as well as to valves, electronics and other equipment – and avoiding non-productive time (NPT).
The value of innovative solutions is clear, with the Norwegian Offshore Directorate pointing to “improvements in field development technology and drilling” as key to future returns.
And under some scenarios mapped in the organisation’s Resource Report 2024, new technology will be crucial to enhanced and expanded recovery from operating and satellite assets.[1]
Evolution
An evolution in downhole tools will facilitate significant savings across the industry, not only through improved efficiency during deployment but also in subsequent operation and production.
In the pursuit of cost savings, a critical objective is to reduce the total number of runs required to remove debris from the wellbore. The dimensions and design of magnets are significant factors that drive positive outcomes in this process.
The goal is a casing magnet ready to tackle the most challenging milling or drilling operations, as well as fishing, workovers and other remedial and intervention tasks.
Cutting edge
The heavy-duty magnet solution developed by Odfjell Technology is a case in point and addresses all of the above through a combination of innovation and proven experience.
UltraMag is designed with an extended length that facilitates a larger magnet surface area. It incorporates longitudinal ribs that securely accommodate rows of high-strength, temperature-resistant rare earth magnets, along with dedicated flow channels.
The tool also features non-rotating upper and lower centralisers that enhance ideal positioning, reduce wear on both the casing and the tools, and optimise the overall efficiency of operations.
With an eye on robust and reliable operations over time, Odfjell Technology further developed detachable magnets that enable a thorough magnetic particle inspection across the entire mandrel. This not only allows compliance with industry standards but reinforces the integrity and reliability of the asset.
Performance
After a year on the market, the UltraMag has achieved over 100 successful deployments for clients both offshore and onshore, primarily in Norway. These deployments are largely focused on milling and whipstock operations.
Clients have noted that this design effectively removes more debris while requiring fewer operational runs, leading to improved efficiency and enhanced safety. The latter is based at least in part on a specialised cleaning tool that efficiently removes collected debris while minimising the risk of injuries to hands and fingers.
Numerous success stories support the evolution of the concept.
Feedback from a leading customer in Norway described the product as excellent following the initial deployment of four 13 3/8 UltraMag HD Casing Magnets in a whipstock run. The client immediately requested preparations for a subsequent 18 5/8 whipstock run.
A major national oil company (NOC) in the Middle East has conveyed its satisfaction with the performance of the 9-5/8” UltraMag, noting that the amount of debris recovered more than doubled compared to results achieved with other third-party magnets. This positive feedback reflects the effectiveness of Odfjell Technology’s solutions in meeting client needs.
The right tool
A clean, safe and efficient operational environment is central to success across oil and gas, particularly when tackling the challenges presented by legacy assets in mature markets including Norway.
Decisions surrounding debris removal in milling, drilling, P&A or wellbore clean-up should feature a solution that offers exceptional strength, efficiency and versatility – where integration into a wider debris management strategy can reduce downtime, lower costs and maintain wellbore integrity.
Reduced time on site, better removal results, minimised risk and a lower carbon footprint – it all starts with the right tool. Which is why Odfjell Technology believes the UltraMag technology represents a significant advancement.
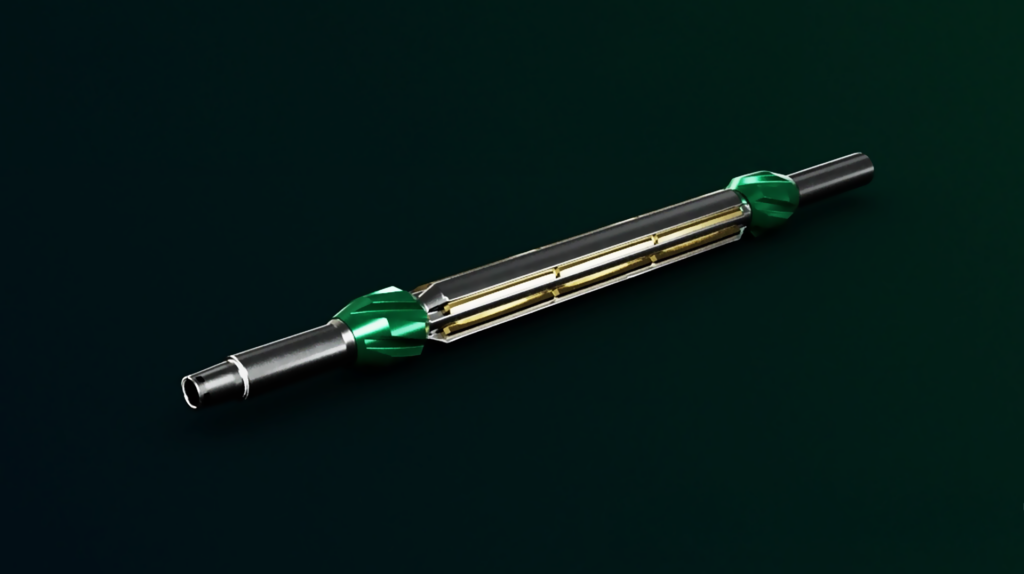
[1] https://www.sodir.no/en/whats-new/publications/reports/resource-report/resource-report-2024/three-potential-scenarios-for-the-ncs-leading-up-to-2050/