Innovative dormant casing scraper toolrewrites rulebook on well services
DrillRdillo provides widest range of benefits to industry in search of proven solutions, writes Ian Low, Well Intervention Product Line Manager with Odfjell Technology Ltd
The oil and gas industry is working smarter than ever as part of wide-ranging efforts to maximise economy, improve efficiencies and boost time savings.
Odfjell Technology Ltd’s DrillRdillo (DRD) dormant casing scraper tool, proven across multiple global plays, provides the next-generation capabilities and robust performance necessary to meet all of these goals. But, more than that, it helps to make a significant contribution to reduced carbon footprints across the crucial projects required to meet demand and security of supply.
The DRD is rigorously tested, fully open-hole compliant, boasts a track record of delivery without failure or pre-shear, and provides operators with confidence across operations including wellbore clean-up, completion, remedial and intervention.
The tool is rightly recognized as the market leader, and is backed by the wider services and products of Odfjell Technology and the entire Odfjell family.
Tried and tested
The DRD is a pioneering 360-degree contact robust scraper tool with retracted blades activated through ball drop and is designed to be run in a drilling string in dormant mode before being put to work within the casing.
It is a proven product with a single-piece body made from high-strength steel and carbide-faced ribs. The DRD has undergone multiple evolutions to create the most reliable, cost-effective, and capable solution available in the market today – saving money, increasing well productivity and maintaining wellbore integrity.
Odfjell Technology has dedicated significant time and resources to testing in high-PVT environments and for the high vibration/oscillation that can be experienced during drilling. Destructive testing included shock testing of the blade retention system with 100 strikes at 600gn and no pre-shear observed, and jarring of the activation system at 300gn, with no deformation or pre-shearing observed.
The DRD has since 2018 proven its capabilities, economy and efficiency across hundreds of applications for the most demanding projects in the harshest of environments.
Proven results
Offshore Brunei, for example, an oil supermajor was seeking to optimise rig time by combining wellbore clean-up (WBCU) and drilling operations in a single run, allowing the gravel pack and upper completion to run right after the drilling BHA was pulled out of the hole – without additional WBCU runs.
Odfjell Technology proposed the 7 inch and 9-5/8 inch DRD drilling scraper to run in tandem with the 8-1/2 inch drilling BHA. Following extensive R&D during development and subsequent successful deployment, the tool was selected as the best option to run in the open without the risk of pre-shearing.
The well was drilled to total depth (TD) at 3120 meters with the DRD kept in the case hole throughout; the survey was also completed in the same run. The bit was then pulled out of the hole (POOH) just above the casing shore, and both DRDs were activated by dropping the activation balls – production packer and GP packer setting depths were then scraped.
The BHA was subsequently tripped down to TD again to displace the open hole with solid free mud before POOH to the casing shoe to displace the case hole with brine.
The results were impressive. The client saved two dedicated WBCU trips, each of which would have taken around 18 hours, totalling 1.5 days of rig time savings or US$240,000. Further, the blades of the DRD only expanded after drilling was completed, reducing the risk of casing wear during extensive rotation.
Ideal solutions
The bottom line, not only off Brunei but in repeated deployments for projects worldwide, is significant reductions in operation times and costs alongside fully optimised safety and quality.
Whether a cement drill-out and cleaning off Norway that saved 18 hours of rig time, a drill-out of a UK North Sea reservoir section and scraping of the lower and upper completion packer settings in a single trip that saving 14 hours of rig time or, off Africa, a single trip to drilling out a bridge plug, cement plugs and WCBU, eliminating the need for a second run – this is innovation in the service of sustainable and dependable results.
The future belongs to those who embrace the best solutions and deploy the tools – like Odfjell Technology’s DrillRdillo – that produce the optimal results while reducing time, saving money and minimising carbon impacts.
Author
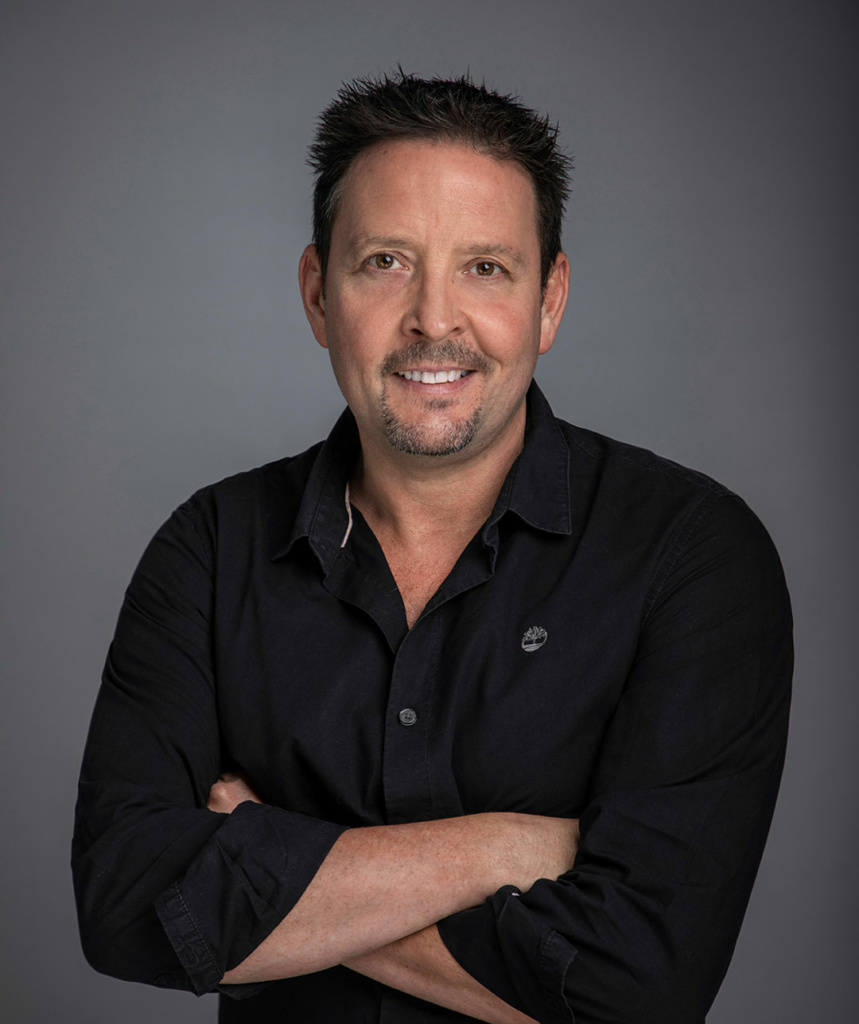
Ian Low
Global Product Line Manager – Well Intervention