Increase casing filling speed with autofill equipment
When running casing, one of the things you always have to keep in mind is keeping the casing string filled with mud.The reason for this is, of course, that you want avoid collapse of the casing.
But filling the casing takes time. Time better spent fulfilling your primary objectives of running the casing to TD, cementing and pressure testing it. The process of filling the casing usually takes between 1 and 1.5 minutes, depending on pipe dimension, pump rates etc. 1.5 minutes is at least a quarter of the time you spend on each connection, so any time saved on this simple task might have a huge impact on the overall operation time.
Four methods of casing filling
There are four main methods that are used to fill the casing:
- Use a hose and simply fill up as required
- Fill directly from the top drive
- Use a dedicated tool (as covered in this article)
- Use autofill floats above the casing shoe
In my opinion, the first option is not preferable. It is time consuming, usually requires personnel to insert the hose into the pipe. And you need to stop the operation in order to fill.
Option number two is somewhat better, but will often result in a messy drill floor, or even problems or delays making up connections as a result of contaminated threads. And again, you need to stop the operation.
Option number three, using a dedicated tool, will usually be your best option. By choosing the correct tool, you can fill the string and, at the same time, avoid the issues related to the first two methods.
Option number four is an often overlooked, or should I say avoided, solution. Using autofill equipment, such as the Halliburton SuperFill, can in some instances be a very good option. First of all because it will remove the need to actively fill the casing. It will allow the mud to flow into the casing through the casing shoe. But it can also provide solution to another issue that can have a big impact on casing running speeds: ECD margins. Reducing the surge pressure produced by running the casing string is vital in order to prevent fracturing formations and/or triggering mud losses.
By incorporating auto filling equipment into the casing design, you can, to a certain degree, avoid the limitations in running in hole speed that you normally would have to live with.
The table below is an example of how severe the limitations can be. As you can see, there are very little limitations in the beginning. As we approach TD, the recommended RIH-speed drops to a mere six meters per minute. You will spend about two minutes running each casing joint in the hole. That is painfully slow.

By using autofill floats you can at least reduce the surge pressure and increase your running speed.
So what’s the catch?
As with most things, autofill equipment has a few drawbacks. First of all it has been considered unreliable as a result of unintentional conversion of the floats. The use of such equipment may also be restricted due to well control procedures. And lastly, the problem of backflow. When running in hole you may experience backflow that will contaminate threads and make a complete mess on the drill floor. The backflow can to a large degree be contained by using an internal filling or circulating tool that will stop or divert the backflow.
Risk vs reward
I guess the limited use of autofill equipment is based on comparing the risk associated with it to the potential gains. Or maybe it’s because of a bad reputation? I don’t know. But in the present situation, one would think that anything (inexpensive) that can enhance your efficiency would be explored and utilized.
Topics: Casing Running
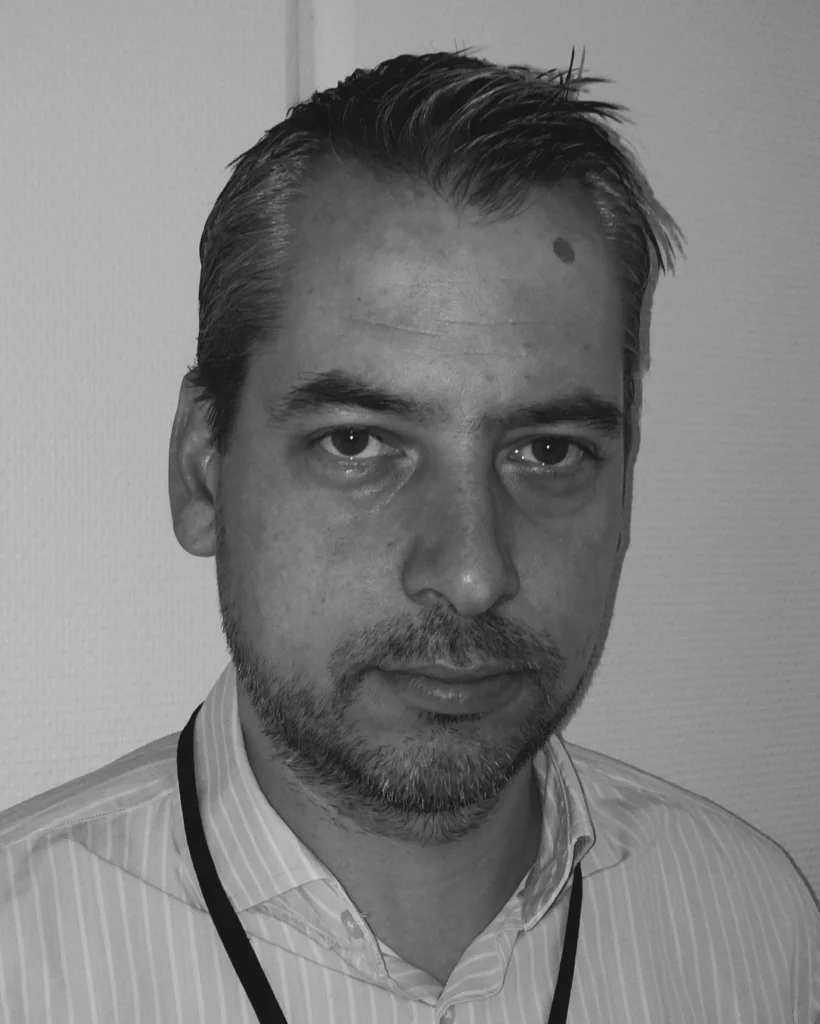
By: Cato Gjesdal
Cato Gjesdal has 10 years’ experience from the oil & gas industry. As Sales & Project Engineer in Odfjell Well Services, he works with clients optimizing and improving tubular running operation such as casing running, P&A, completions and well testing.