How to reduce offshore risk during tubular running services
Running casing, by its very nature, can be a dangerous occupation with many pitfalls to be aware of. Contrary to popular belief, most accidents are preventable, which is why we must be aware of the hazards and take every precaution necessary by implementing the stringent safety measures while avoiding injury to personnel on the rig site.
Identifying risk, with an associated understanding of possible accident scenarios and consequences, represents the basis for all safety work. The most common risks associated with running casing offshore are injuries to hands and fingers, musculoskeletal injuries, hearing injuries, being struck by falling objects, exposure to hazardous chemicals and movements of heavy equipment while working in the red zone.
Knowledge and deep understanding of these risks is crucial to developing and implementing the right mitigating actions in order to prevent accidents and injuries. We focus on human, technology and organizational factors to develop effective preventive measures.
Obviously, there are a lot of things that can be done in advance of the operation, and before the casing personnel is sent to the rig. This can be proper training, use of skilled personnel, accurate and adequate information about the job that shall be done etc. But;
How can we reduce risk during casing running?
As mentioned above, risk is a product of probability multiplied with consequence. To reduce the risk, we can implement measures that reduce either the probability for an injury to occur, or we can implement measures to reduce the consequence if, after all, the injury should occur.
We need to do something with the probability first (preventive barriers), and then we need to focus on the actions that reduces the consequence (reactive barriers). Professor James Reasons’ “Swiss Cheese model” of accident causation, is a model used to show how lack of barriers results in risk for accidents.

To establish a barrier, we need to implement measures. For each barrier to work, the implemented measures should be based on the three elements; Man, Technology and Organization (MTO):
Man: What can the casing personnel do to reduce risk?
- Perform a pre-job meeting to review the hazards, identified in the SJA, with the crew, and plan the job. Before beginning work, communicate the hazards within the crew.
- Complete a thorough safety job analysis – Before a shift starts, together with the drilling crew, collectively review and analyze your tasks to be performed. Ensure you discuss any potential hazards involved and actions needed to eliminate or reduce the risk of injury.
- Engage your mind before your hands – Protect your hands. On casing jobs, most hand injuries result from unsafe work practices and misplaced hands. Use caution and gloves appropriate for the job at hand.
- Be aware of walking and working surfaces – Slips, trips and falls are best avoided with good housekeeping. Keep walkways clear of tools (welding leads, extension cords, etc.) and debris; clean spills immediately, and make it clear others are expected to do the same.
- Safely operate heavy equipment – Casing crew must be aware of moving equipment above and at the rig floor. Especially of simultaneous operations that take place by a multitude of contractors, sub-contractors, clients and other involved parties.
- Ensure hand and power tools are in proper working order – All hand and power tools – from hammers and pipe wrenches to pneumatic, electrical and hydraulic equipment – must be inspected before every use. Inspect all components for cracks, leaks, cuts or excessive wear.
- Practice good ergonomics. Be aware of body positioning during pulling, pushing and lifting heavy equipment, and practice the buddy system for heavy lifts.
- Understand and follow safe practices for chemical handling – When handling chemicals, ensure you are familiar with the safety data sheet and the information concerning what to do in case of an emergency.
- Follow safe operational procedures
- Use proper personal protective equipment – Wear protective equipment meant to protect you from injury or illness. Eye and hearing protection, safety boots, gloves and hard hats should always be worn on rig sites.
Technology: What technical measures should be in place to reduce the risks during casing operations?
- Develop and use remote operated running and handling equipment, such as pipe handling systems, elevators, slips, stabbing systems and tongs.
- Remote operated equipment places the crew outside of the danger zone (red zone), away from the equipment movements and away from the path of falling objects. Ergonomic injuries are eliminated by operating the control panel instead of wrestling heavy equipment. Fall, slips and trips become obsolete while crew stands on the side lines to operate the equipment.
Organization: How can the organization reduce the risks during casing running?
- Create a risk register – Get first-hand information by involving the rig site crews in identifying the hazards involved in casing running. The results of the risk assessments are documented in the risk register, and it is crucial that this is communicated to all personnel.
- Verifying that all procedures for running, handling and break-out of tubulars are well known to the rig site crew and equipment rig up and rig down checklists are completed.
- Safety campaigns are a good way to get crews to focus on protecting themselves from injury.
- Have an open working environment to be able to communicate, talk about issues, solve problems, share experience etc.
- Develop a reporting culture where personnel are engaged to report any incidents, near misses, conditions, non-conformances and proposals for improvements. Follow up corrective and preventive actions and perform inspections, audits and verifications.
Statistically, injuries are on the decline. The key to reducing risks is to understand how and why accidents happen and have technology, administrative tools and competence in place to mitigate the risks. The introduction of the “zero philosophy” is a milestone in terms of attitudes. This mindset can be summed up in the statement that accidents do not happen, but are caused. All accidents are therefore preventable, so that the goal will be zero injuries and accidents.
See also: How offshore experience prevents us from making the same mistake twice
Topics: Casing Running
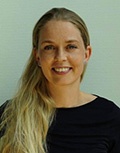
By: Stine Bøen
Stine Bøen has 10 years of experience from the oil and gas industry, working as a quality, health, safety and environmental (QHSE) professional. She is part of the OWS management team in Norway, and among other things, works with QHSE performance monitoring, auditing, managing risk, investigating and following-up incidents and continuous improvement of management systems. Stine has a master degree within Societal Safety.