Can Robotics on Rig Floor Make a Difference in Drilling Performance?
In a previous blog we have described the significant potential efficiency gain that lies in a fully automated drilling process, by use of intelligent robots at the drill floor. Before we go into details about how such a system could look, and how we can get there, let’s take a look at where we are on automation on our modern 6th generation rigs today.
What is automation?
Wikipedia defines automation as “the use of various control systems for operating equipment … with minimal or reduced human intervention”. For decades we have talked about automation in the drilling industry, and you will often find terms like “fully automated” or “high degree of automation” when we and others describe our rigs. How come then that a rig crew still counts just as many as in the 70’s and we are still not able to drill faster than we did 40 years ago?
For sure we have removed many manual rig floor operations, and the rigs have become incredible sophisticated, but still we are struggling to realize the cost savings and efficiency gains that other industries, like the manufacturing and processing industries, successfully have achieved in the same time period.
Degrees of automation in a drilling package
A 6th generation offshore drilling rig operation still has a mixture of everything from simple manual operations to sequences of advanced automation. Below is a categorization of the different levels of automation along with some practical examples found on board.
Level of automation | Description | Application on a modern rig floor | |
---|---|---|---|
0 | Manual operations | Tasks that are not fully mechanized Active human interference on rig floor | Handling and spinning of x-overs and subs Handling of Kelly Cock Handling of stabilizers Handling of hole cover + a number of other operations |
1 | Remote controlled machines | Mechanized tasks Humans actively operating via remote controls or commands | Set & release slips with slips lifter Drill floor manipulator arms |
2 | Remote controlled machines with sensors and logics | Sensors and logics can end or halt the operation(e.g. with load and position sensors/anti-collision systems, load cells etc.) | Move roughneck to and from well center Make up drill pipe to preset torque Make up casing to preset torque |
3 | Remote controlled machines with logics and sequences | Mixture of preprogrammed sequences, manual commands, sensors and logics that controls one or more machines | Pipe handling from rack to well center Make up pipe with iron roughneck Anti-collision systems that halts the operation before collision |
4 | Fully Automatic Machines | Preprogrammed sequences that completes a task without human input as long as everything goes according to plan | Auto-trip systems Auto-drill systems |
5 | Autonomous machines | A machine that is capable of sensing its environment and operating without human input, and that are capable of adapting to changes of plan | Intelligent machines/robots with integrated motion planning that can adapt to the other machines’ movements on a rig floor by making their own decisions, for example on motion planning |
Not only tripping and drilling
An operation on board a 6th generation drilling rig will most of the time involve operations categorized as level 0 to 3.
Automatic systems for tripping and drilling might bring you to level 4, however, these solutions are still immature and often not used by the drill crew even if it is installed. And even more important, they only apply to operations that account for a fraction of the time spent on the well construction.
One of the reasons why we have not seen much improvement in drilling performance resulting from the automation is that the main benefit of moving tasks from level 0 to 3 is in HSE. No doubt that the “hands off technologies” introduced have made our drilling rigs a safer work place. However, if we are going to realize the increased productivity we have seen in other industries, we need to make the steps all the way to level 5.
Going from level 3 to level 4 might give us 10% better performance than today, but the big impact will come when we get to level 5. Not only for the tripping and drilling phases, which typically account for around 30% of the time in a deep water operation, but for all phases in the well construction process.
Is bigger better?
One of the main recent developments in offshore drilling rig design is that things have turned bigger. The drilling packages have grown in width from single derricks to dual derricks, and in height from single and double stands, to triple and quadruple stands. But we still only drill one well at the time meaning that everything that goes into or out of the well need to pass the main rotary table – on critical path…
It is obvious that if you can develop a more efficient operation in your “main” derrick, you may also allow for down-scaling of your drilling package on board the rigs. You might not improve radically on the tripping and drilling speed compared to a 6th generation dual derrick (and bear in mind this is only representing 30% of the time spent constructing a well – there is still significant potential to make the other 70% of the time more efficient even on board the 6th generation rigs), but a fully automated drilling package with autonomous machines will allow down scaling to smaller derricks which again will require smaller rigs. This will again reduce the CAPEX, the day rate and eventually drive down the well cost. In parallel, older and less efficient rigs may be retrofit with a more efficient package to match 6th generation performance.
We believe that the key to achieving the step change in well construction cost that our industry desperately needs to stay competitive lies in automation and implementing autonomous, robotic equipment and systems in the drilling process. In my next blog I will take you through how such a system could look like.
Topics: Drilling Equipment, Drilling
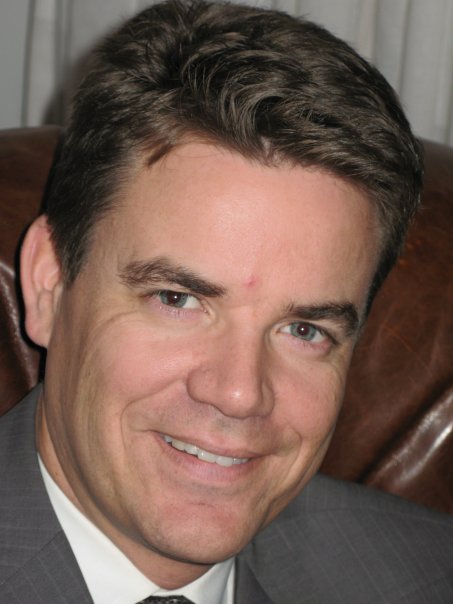
By: Per Lund
Per has 20 years’ experience from operations, technology development, business development and management positions in the oil and gas industry. His background is from well services, well abandonment and subsea services, working across Europe, Gulf of Mexico, Middle East, Africa and Asia. Per is Senior Vice President – Innovation and special projects in Odfjell Drilling.