A novel approach to casing preparation after drilling
With increased well costs, particularly in deepwater wells, the benefits of combining operations in one trip are too good to ignore. With new advances in technology it is now possible to combine what was two trips into one, saving considerable time and money. Your drilling bottom hole assembly (BHA) can now be designed to allow casing preparation operations to be performed immediately post drilling.
The long way: Conventional methods
Historically a dedicated trip would be carried to prepare the lower completion packer/liner setting depths after drilling the previous hole section. This would use current casing scraper & brush technology. In deepwater wells this could add significant rig time and cost. What if we could give the drilling team a new methodology to reduce the time & cost in one run instead of two?
The short way: Casing scraping and drilling in one run
New developments in scraper technology now allow all operations to be carried out in one trip. Such technology can be run integral to the BHA, allowing the hole section to be drilled without compromising drilling efficiency.
Once the section is drilled, simply pull out to the required depth, activate the drilling scraper and prepare the packer / liner hanger setting area. Then simply pull the work string out of the well. Now just run in your lower completion and set in place. You have just saved potentially 24hrs rig time.
The tools in an ideal scraping-drilling BHA
1. Casing scrape
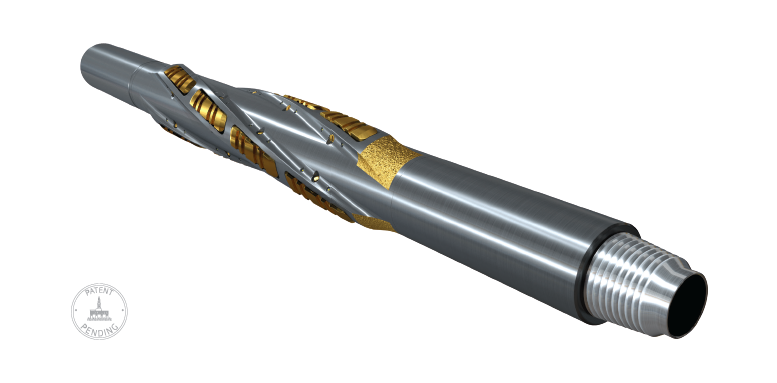
A new type of scraper design, such as the DrillRdillo™ Drilling Scraper, from Odfjell Well Services, allows the Operator to immediately prepare the packer/liner hanger setting depths post drilling.
This casing cleaning tool eliminates the need for a dedicated scraper run and reduces time between drilling and running completions.
Whilst conventional casing brushes and scrapers always are in active mode, sophisticated drilling scrapers are designed to run in a switched-off mode whilst drilling the open hole section.
The scraping elements are retracted within the body to prevent damage or sticking during drilling operations and can be activated when desired, by simply dropping a ball to change the tool state.
2. Casing magnet
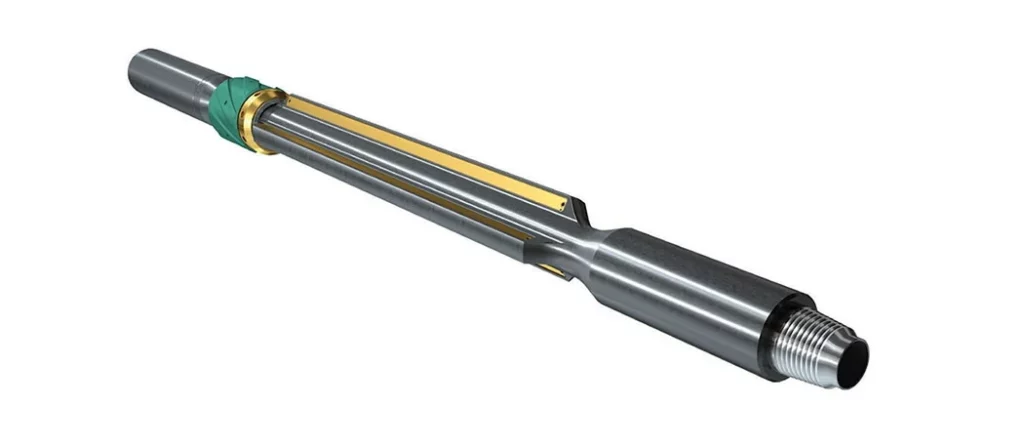
Debris recovery tools, like the MAGStar4™ HD Casing Magnet, are robust, high strength debris collectors adapted to suit any casing size and drill pipe combination.
Whilst tripping or circulating, the magnets will attract ferrous debris from the wellbore and capture it for removal at surface.
Drill string schematics
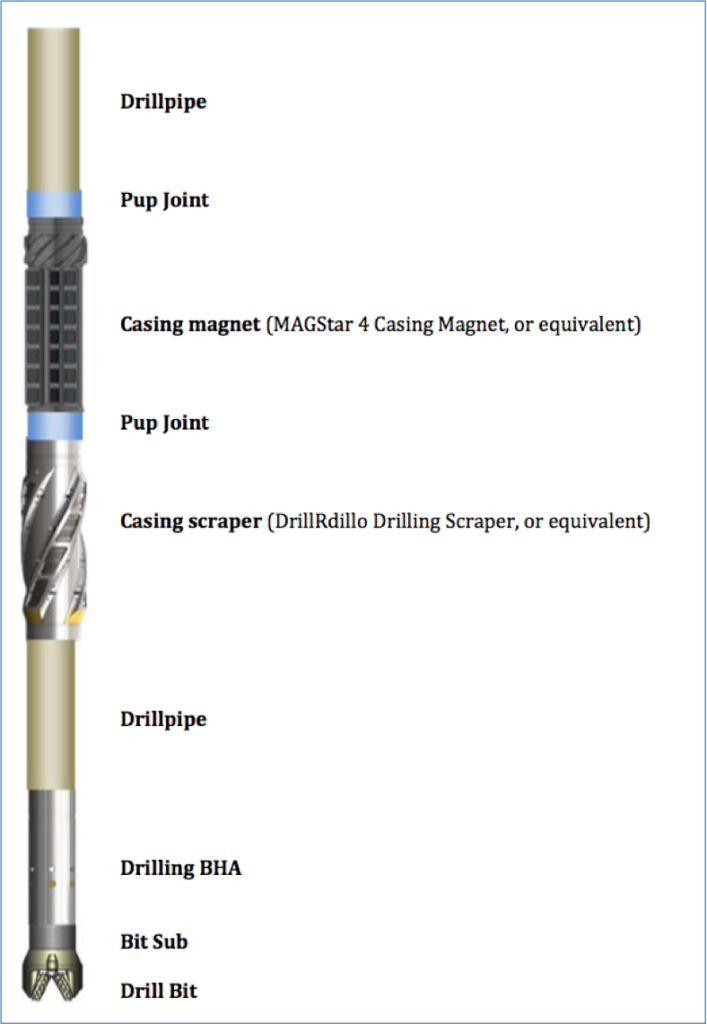
What are your thoughts or comments? If you want to learn more about wellbore clean-up best practices, be sure to download our e-book on the subject.
Topics: Wellbore CleanUp, Casing Preparation
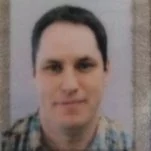
By: Stephen Mair
Stephen has over a decade experience in WellBore CleanUp (WBCU) activities ranging from authoring industry best practices to WBCU research and development projects. With experience in various global locations (North Sea, Europe, Africa & Alaska) he has been involved in introducing the next generation of mechanical & software solutions to meet today’s WBCU challenges.